HYDROPHOBICITY AND ACTIBACTERIAL PROPERTIES
We wanted to make our Bio Cocoon super hydrophobic in nature.
-
Hydrophobic means water repellent and not water resistant
-
Hydrophobicity on a material can be calculated by the contact angle between surface against the water and it should be more than 150°.
-
It is found Betulin a natural compound from Birch tree has both hydrophobic and antibacterial properties. It shows a static water contact angle of 136° and an antibacterial property with a bacterial removal of 99%.
-
Considering these two aspects, we believe it is possible to fabricate a betulin-attached cellulosic textile with improved hydrophobicity as well as antibacterial property.

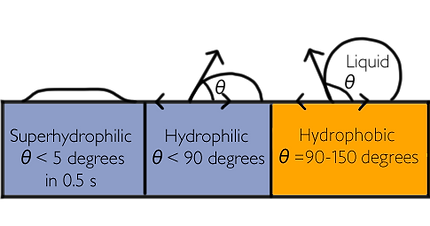
EXPERIMENTING MATERIALS
We can either use existing material/fabric (100% cotton) or make our own material. We chose to make a biodegradable textile and then make it hydrophobic and antibacterial.
​
​
​
​
​
​
​
​
​
​
​
​
-
Cellulosic Material: Betulin was extracted from birch outer bark by Soxhlet extraction for 48 hours.
​
​
​
​
​
​
​
​
​
​
-
After solvent evaporation and drying, betulin was obtained as a white powder with a purity of ca. 80%
​
​
​
​
-
Betulin based copolymer is derived by synthesizing betulin and Terephthaloyl chloride (TPC) in a toluene solution.
-
The mixture is then heated and cooled at ambient temperature.
​
​
​
​
-
Betulin copolymer is introduced onto the textile surface by esterification process.

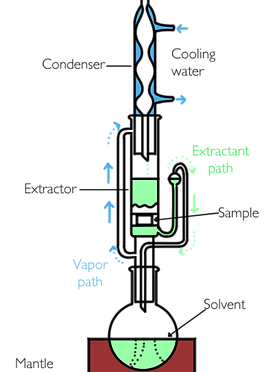
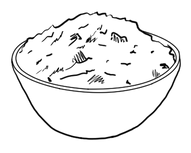


MAKING OUR OWN NATURAL SYNTHETIC FIBRE
Fibre: Polylactic Acid fibre (PLA, Long sugar chain molecule)
PLA is the biodegradable natural polymer and is available in nature in the form of starch rich products. We chose Banana as our starch product since it is abundantly available in Australia and easy to source.
​
Raw Material: Banana
The main component of unripe bananas is starch. The rhizome, pseudo stem and banana peel have high starch content and can be used in the process.
Green bananas have 70-80% starch.

MANUFACTURING PROCESS OF PLA
• Starch: CO2 & water from atmosphere is converted into starch. This starch is readily extracted from plant matter and converted to a fermentable sugar by enzymatic hydrolysis (Amylase)
​
​
​
​
​
​
​
​
​
​
​
​
​
​
​
​
• Lactic Acid: PLA is composed of lactic acid which is produced by converting banana starch into sugar and then fermenting it to yield lactic acid.
​
​
​
​
​
​
​
​
​
​
​
​
​
​
​
​
• Polylactic Acid: Polylactic acid is derived polymerisation to form long-chain polymer molecules of lactic acid.
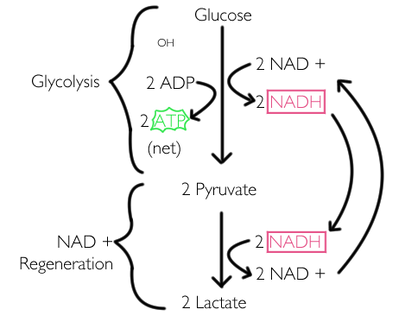

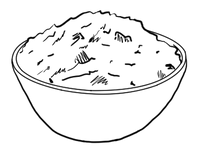

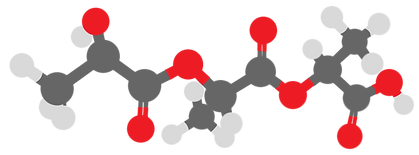
SPINNING THE PLA INTO A YARN
-
PLA is converted into long-chain molecule fibres with the help of extrusion and then spun into a yarn.
​
-
This yarn is then subjected to a double knitting process to produce textile.
​
-
This textile is dipped into the betulin solution bath to complete the process of acquiring the required properties with the help of bio design.
​
​
​

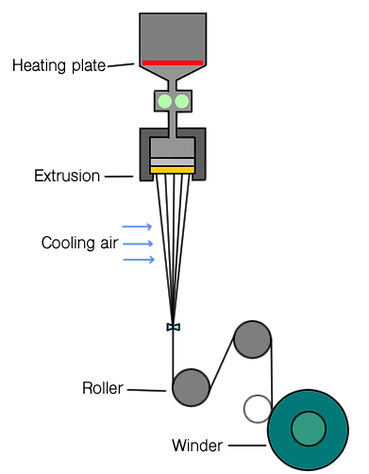
Yarn double knitted into textile and then dipped into betulin bath to make it hydrophobic and antibacterial on the inside.
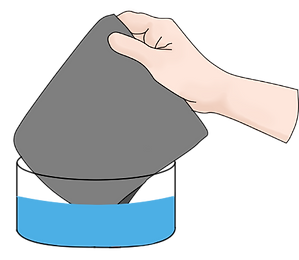

TEXTILE READY TO BE MADE INTO A BIO-COCOON
-
The natural fibre is made into a textile with the process of double knitting for the required thickness and warmth.
​
-
It becomes hydrophobic on the external surface when dipped into the betulin bath.
​
-
It is then cut and sewn to form the designed prototype.
​
-
The bio-cocoon is bio-degradable in the presence of a specific bacteria named amycolatopsis and saccharotrix.
​
​
​